When optimizing the milling effect, the blade of the milling cutter is another important factor. In any milling, if there are more than one blade participating in the cutting at the same time, it is an advantage, but too many blades participating in the cutting at the same time is a disadvantage. When cutting, it is impossible for each cutting edge to be cut at the same time. The required power is related to the number of cutting edges participating in the cutting. In terms of chip formation process, cutting edge load and processing results, the position of the milling cutter relative to the workpiece plays an important role.When face milling, use a milling cutter that is about 30% larger than the cutting width and position the milling cutter close to the center of the workpiece, then the chip thickness does not change much.The thickness of the chips cut in and out is slightly thinner than the thickness of the chips cut in the center.
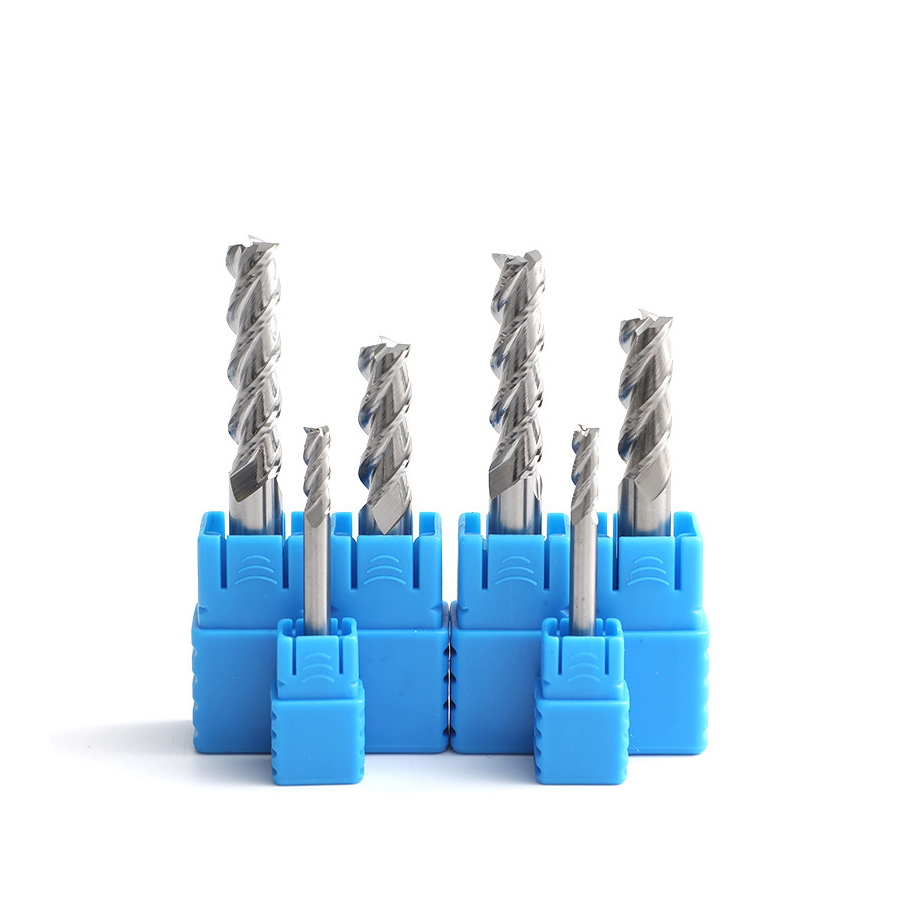
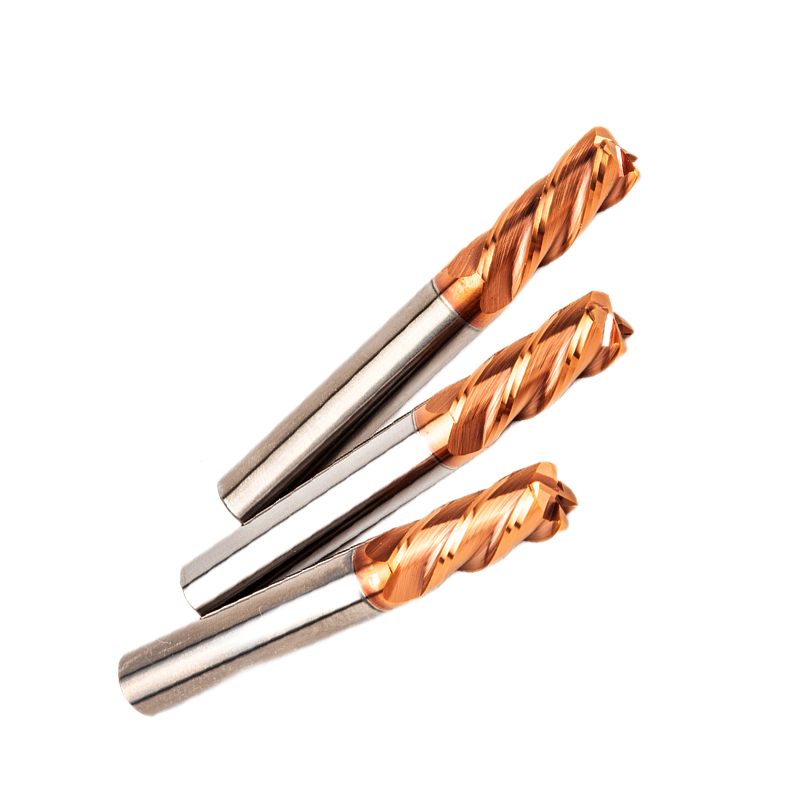
In order to ensure that a sufficiently high average chip thickness/feed per tooth is used, the number of milling cutter teeth suitable for this process must be correctly determined.The pitch of a milling cutter is the distance between the effective cutting edges.According to this value, milling cutters can be divided into three types-dense tooth milling cutters, sparse tooth milling cutters, and extra-dense tooth milling cutters.
Related to the thickness of the milled chips is the main declination angle of the face milling cutter. The main declination angle is the angle between the main cutting edge of the blade and the surface of the workpiece. There are mainly 45-degree, 90-degree angles and circular blades. The direction of the cutting force changes greatly with the main declination angle: Milling cutters with a main declination angle of 90 degrees mainly produce radial force, acting in the feed direction, which means that the machined surface will not withstand excessive pressure, which is more reliable for milling workpieces with weak structures.
The radial cutting force and axial direction of a milling cutter with a main declination angle of 45 degrees are roughly equal, so the pressure generated is relatively balanced and the power requirements of the machine tool are relatively low. It is especially suitable for milling short-chip material workpieces that produce broken chips.
A milling cutter with a circular blade means that the main declination angle changes continuously from 0 degrees to 90 degrees, which mainly depends on the depth of cutting.The cutting edge strength of this blade is very high. Because the chips generated along the direction of the long cutting edge are relatively thin, it is suitable for a large feed. The direction of the radial cutting force of the blade is constantly changing, and the pressure generated during the processing process will depend on the depth of cutting.The development of modern blade geometry and groove shape makes the circular blade have the advantages of stable cutting effect, low power demand for machine tools, and good stability.It is no longer an effective rough milling cutter, and it is widely used in both face milling and end milling.
Post time: Nov-11-2022