The birth of the world's power tools began with electric drill products-in 1895, Germany developed the world's first direct current drill. This electric drill weighs 14 kg and its shell is made of cast iron. It can only drill 4 mm holes on steel plates.Subsequently, a three-phase power frequency (50Hz) electric drill appeared, but the motor speed failed to exceed 3000r/min.
In 1914, an electric drill driven by a single-phase series-excited motor appeared, with a motor speed of more than 10,000 rpm.
In 1927, an intermediate frequency electric drill with a power supply frequency of 150~200Hz appeared. It not only has the advantages of high speed of a single-phase series-excited motor, but also has the advantages of simple and reliable structure of a three-phase power frequency motor. However, due to the need for intermediate frequency current power supply, the use is limited.
In the 1960s, battery-type electric drills without power cords that used nickel-cadmium batteries as power supplies appeared.By the mid-to-late 1970s, due to the reduction in battery prices and the shortening of charging time, this kind of electric drill was widely used in Europe, America and Japan.
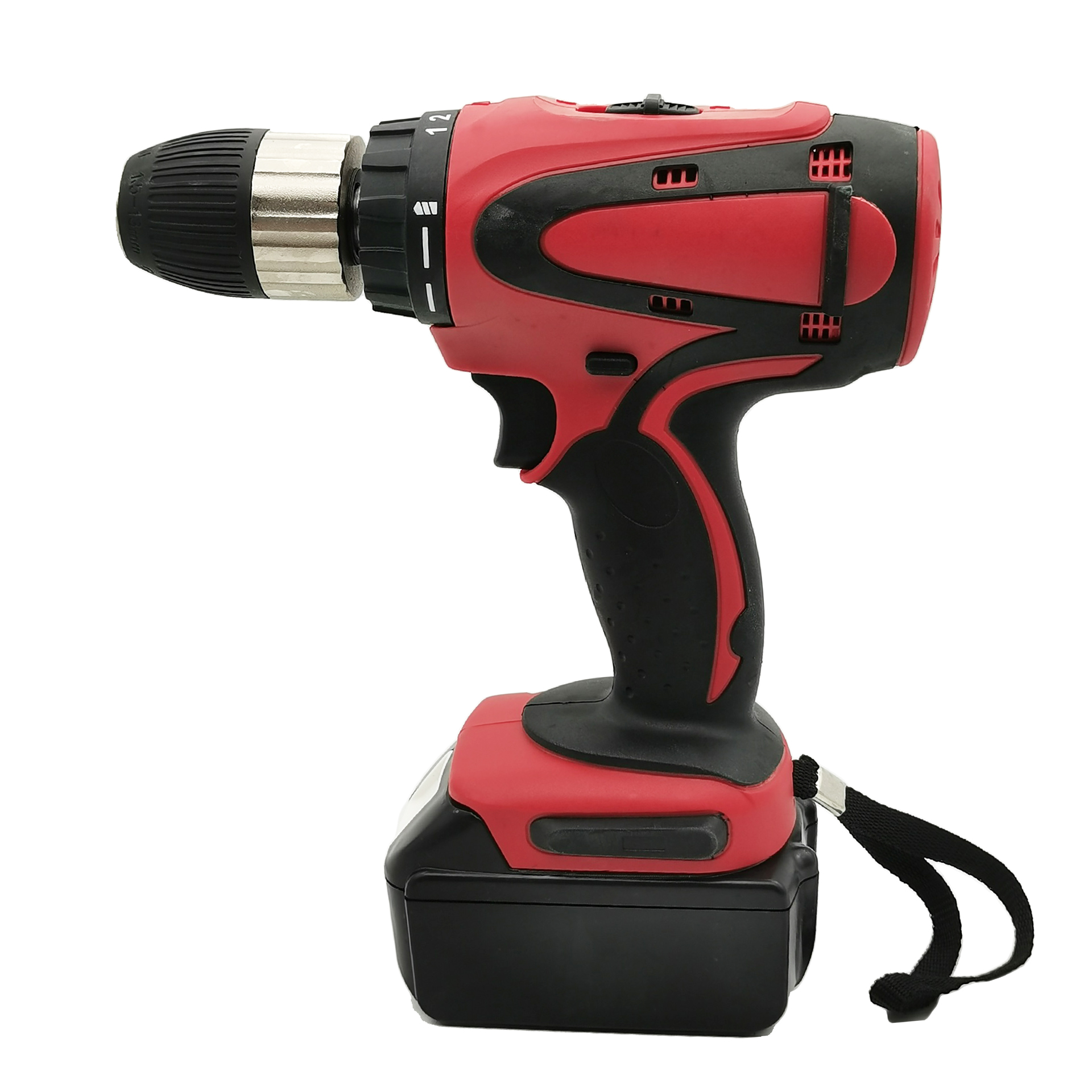
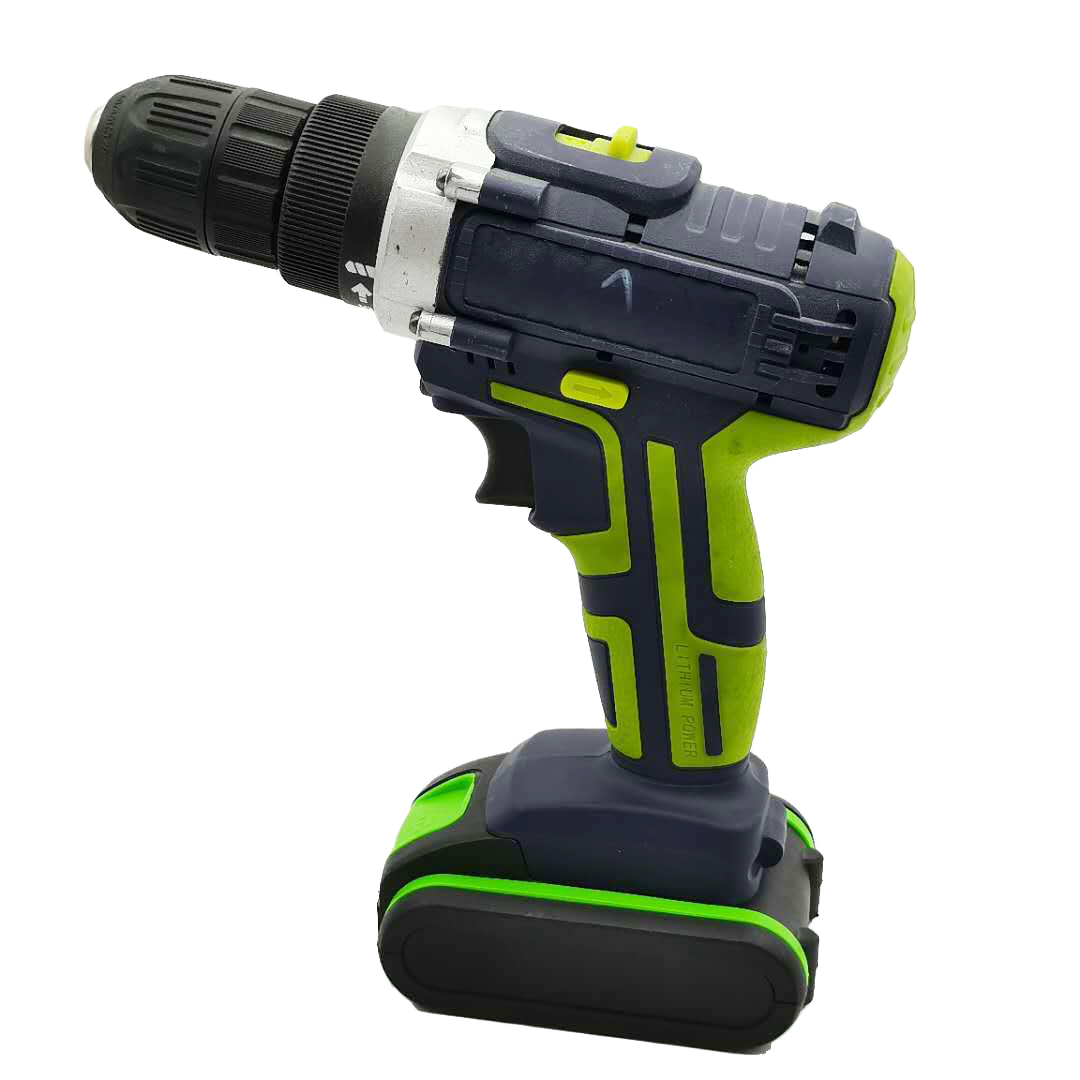
The electric drill originally used cast iron as the shell, but then changed to aluminum alloy as the shell.In the 1960s, thermoplastic engineering plastics were applied to electric drills and the double insulation of electric drills was realized.
In the 1960s, electronic speed-regulating electric drills also appeared.This kind of electric drill uses thyristor and other components to form an electronic circuit, and the speed is adjusted by the different depths at which the switch button is pressed, so that the electric drill can be used according to the different objects to be processed (such as different materials, drilling diameters, etc.), choose different speeds.The working principle of an electric drill is that the motor rotor of an electromagnetic rotary or electromagnetic reciprocating small-capacity motor does magnetic field cutting and operation, and drives the operating device through the transmission mechanism to drive the gear to increase the power of the drill bit, so that the drill bit scrapes the surface of the object and better penetrates the object.
Post time: Oct-28-2022